Category
- Products
-
- Contact us
Home » Motor control » Using Soft Starter for starting heavy electrical loads
Using Soft Starter for starting heavy electrical loads
In my practice I have used soft starters to start the water pumps and fans with power up to 200 kW at 400 V. It is excellent solution - slow start, soft stop and less starting current. Manufacturers of soft starters generally recommend using it for different pumps and fans.
Can we use of soft starters (instead of the classic star/delta start) for starting heavy mills for stone, plastic or cereals (power up to 200 KW at 400 V, speed 1400 or 2900 rpm? The goal is reduce starting current to avoid breaching limited peak load.
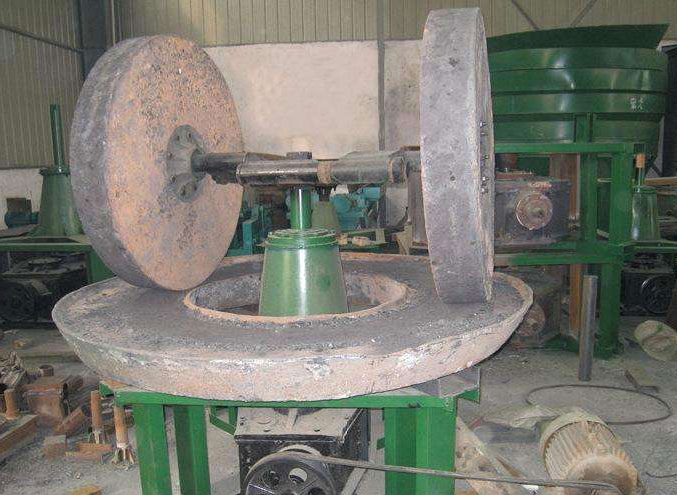
Soft starters are generally different from Variable Frequency Devices (VFD) in, that they do not change the frequency to the motor, but just reduces the available effective current, to reduce the starting torque, and "soften" the start.
A VFD, however, will modify the power to the motor, such that both frequency and effective current are reduced for a gradual startup. This can therefore provide the required torque (current dependent) at a reduced frequency and voltage, so the motor can start up with a reduced power requirement, and therefore also reduced load on the supply network.
My experience in this regard has mainly been with MUCH larger drives, for which a wound rotor motor was preferred in the past, and a variable rotor resistance, in order to provide both the increased torque required, and a smooth acceleration.
Can we use of soft starters (instead of the classic star/delta start) for starting heavy mills for stone, plastic or cereals (power up to 200 KW at 400 V, speed 1400 or 2900 rpm? The goal is reduce starting current to avoid breaching limited peak load.
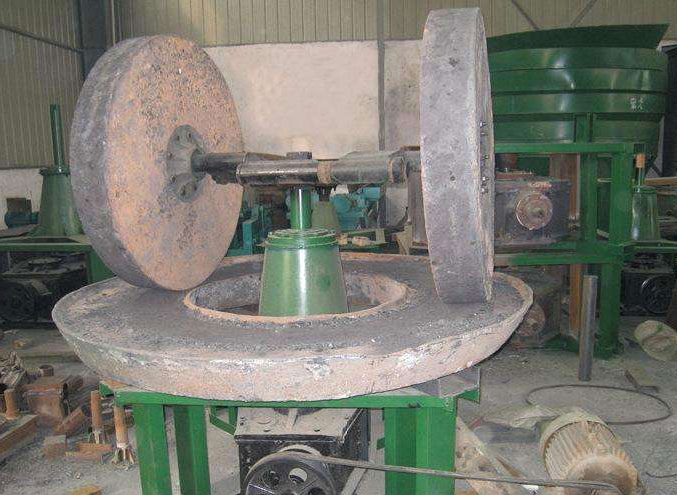
Soft starters are generally different from Variable Frequency Devices (VFD) in, that they do not change the frequency to the motor, but just reduces the available effective current, to reduce the starting torque, and "soften" the start.
A VFD, however, will modify the power to the motor, such that both frequency and effective current are reduced for a gradual startup. This can therefore provide the required torque (current dependent) at a reduced frequency and voltage, so the motor can start up with a reduced power requirement, and therefore also reduced load on the supply network.
My experience in this regard has mainly been with MUCH larger drives, for which a wound rotor motor was preferred in the past, and a variable rotor resistance, in order to provide both the increased torque required, and a smooth acceleration.
We had 180 Kw LT - Dust suppression fan drive with DOL feeder (class 10 OLR and contactor arrangements).. While pre Commissioning we found that the OLR class not suitable.. So replaced with class 30.... And we commissioned (in winter) .... After N no of operations.. Fan tripped on starting itself... ( in summer).. Due to fan startup time temperature raise frm ambient was changed..... Then we replaced with AC drive for smooth operation... Particularly for fan load AC drive are too good
I design Cement plant and heavy mills for stone are the worst load you can have to deal with. You need to provide high torque on a limited peak load source. Only VFD can do the job. Sometimes, the starting torque exceed 150% and need to oversize the motor and the drive to obtain 250% starting torque. In this case, the Normal Running Load (NRL) cannot be used to define the motor and VFD rating.
Rock crushers I have met have not started into load. For planned shutdowns, the feed is stopped before the crusher is stopped, so that it is empty when it restarts. For forced outages / trips, they were manually emptied. I don't have a lot of experience with mills but those I have met were regularly started with a full mechanical load, and had no provision to unload them after a trip. A soft starter is more likely to be suitable if the starting condition is unloaded.
Post a Comment:
You may also like: