Category
- Products
-
- Contact us
Home » Soft Starters Knowledge » Soft Starter working stage
Soft Starter working stage
The Ramp stage
A. For Open loop Configuration
From the instant that the start command is given, the system first imposes a fixed delay (3 to 300/500 ms) for self monitoring, and then causes a voltage to be applied to the motor terminals to achieve the break-away torque.
This is the pedestal voltage in the figure below. This voltage is then ramped up linearly providing a step less increase of motor terminal voltage from the pedestal upto the maximum voltage. At the end of the ramp period the motor terminal voltage is equal to the input power supply voltage. As a standard the pedestal voltage is 40% of the supply voltage. This can however be changed to suit desired applications.
The current drawn by any motor accelerating from the rest position in an open loop configuration depends upon the selected ramp. Shorter the ramp time, greater the peak starting current. Why choose one ramp time rather than another?
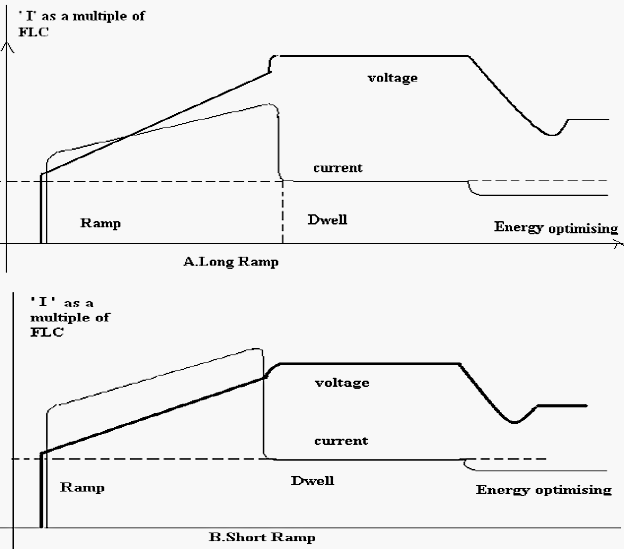
Pedestal voltage; Top: Long ramp; Bottom: Short ramp
For every motor and driven load system, there is a natural ramp at which the acceleration of the load and the motor matches the rate of increase of the output voltage of the soft starter. Selecting a short time will increase the rate of acceleration and the starting current drawn; a longer time will prolong the time before the load reaches the full speed, and will reduce the starting current.
This may be an advantage depending upon the particular application and perhaps on what is convenient for matching with related process equipment.
B. Closed loop Configuration
This configuration of the Soft starter is used in applications where the driven load has a particularly high inertia else it is difficult to start. For example, in a stir application where the medium is glutinous and stiff at the beginning of the process.
The acceleration time of such loads is apt to lag behind the rate of rate increase of ramp voltage even if a long ramp time is chosen. With such loads it may however be necessary to select short ramp time to ensure sufficient starting torque. A short ramp will raise the voltage quickly but the nature of the load prevents the motor speed matching it. The result may be excess current demand.
This problem is over come by a current limit feature which stops the ramp when the current output reaches a pre-selected limit. The ramp is then held until the current falls naturally. The current limiting feature is active only during the ramp period of the soft start sequence. Closed loop control requires continuous measurement and feed back of the current delivered to the motor terminals by using a CT.
The Dwell period
The dwell period begins when the output voltage reaches maximum and this period is equal to the selected ramp time, approximately equal to 10 seconds.
The dwell period maintains a constant voltage at maximum to allow the time for the motor and its driven load to settle to a steady state after acceleration is complete and before the Soft starter automatically enters the energy optimizing mode.
The optimizing stage
The energy optimizing stage is the normal operating condition of the Soft starter when the motor is up to rated speed and driving the load at whatever torque output is demanded. The energy optimizing stage is continuous after the dwell period until a stop command is given.
During the ramp period the system computes a reference value of the power factor. For energy optimizing this value is continuously compared with the running power factor. From the comparator output the system continuously computes, adjusts and updates the firing points of the thryistors so that the total energy delivered to motor corresponds to the load torque demand without wasting energy in overfluxing the motor. The power factor at the supply terminals is in this way maintained at the highest possible value for every condition of the load demand.
Management of the power factor in no way detracts from the capability of the motor to respond to the load demand .The motor performance is unaffected. This feature of the Soft starter is a purely electric function which has the effect of ensuring that at all times the motor delivers the torque demanded, but is allowed to draw only the precise amount of magnetizing current required to support the torque output.
Without this feature, the motor would draw a maximum magnetizing current regardless of the load.
The effect of the energy optimizing function is a cumulative economy in energy consumption.
The Soft-Stop function
This is a unique feature of the Soft starter. Its effect is to prevent an undesirably sudden deceleration of the load. It is useful in various mechanical handling and conveyor systems and in many hydraulic pumping operations where a sudden removal of the drive input can induce undesirable effects, such as the fluid hammer in the pipelines.
The soft stop ramp operates to reduce the motor terminal voltage down to 40% of maximum, at which time, the thyristors are disabled. The motor and load will coast to standstill.
A. For Open loop Configuration
From the instant that the start command is given, the system first imposes a fixed delay (3 to 300/500 ms) for self monitoring, and then causes a voltage to be applied to the motor terminals to achieve the break-away torque.
This is the pedestal voltage in the figure below. This voltage is then ramped up linearly providing a step less increase of motor terminal voltage from the pedestal upto the maximum voltage. At the end of the ramp period the motor terminal voltage is equal to the input power supply voltage. As a standard the pedestal voltage is 40% of the supply voltage. This can however be changed to suit desired applications.
The current drawn by any motor accelerating from the rest position in an open loop configuration depends upon the selected ramp. Shorter the ramp time, greater the peak starting current. Why choose one ramp time rather than another?
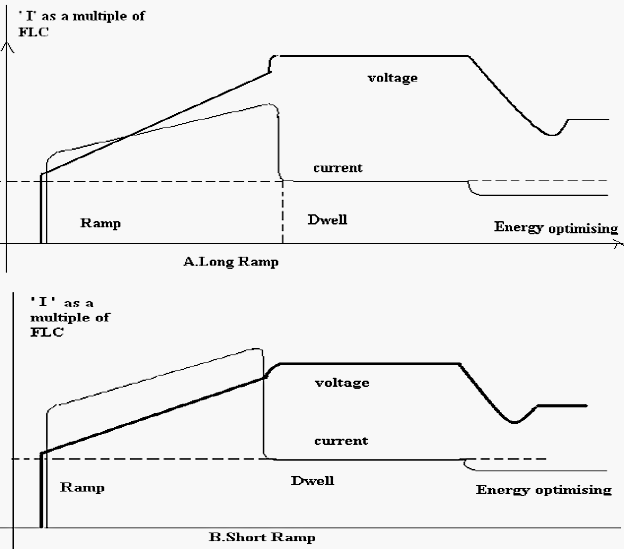
Pedestal voltage; Top: Long ramp; Bottom: Short ramp
For every motor and driven load system, there is a natural ramp at which the acceleration of the load and the motor matches the rate of increase of the output voltage of the soft starter. Selecting a short time will increase the rate of acceleration and the starting current drawn; a longer time will prolong the time before the load reaches the full speed, and will reduce the starting current.
This may be an advantage depending upon the particular application and perhaps on what is convenient for matching with related process equipment.
B. Closed loop Configuration
This configuration of the Soft starter is used in applications where the driven load has a particularly high inertia else it is difficult to start. For example, in a stir application where the medium is glutinous and stiff at the beginning of the process.
The acceleration time of such loads is apt to lag behind the rate of rate increase of ramp voltage even if a long ramp time is chosen. With such loads it may however be necessary to select short ramp time to ensure sufficient starting torque. A short ramp will raise the voltage quickly but the nature of the load prevents the motor speed matching it. The result may be excess current demand.
This problem is over come by a current limit feature which stops the ramp when the current output reaches a pre-selected limit. The ramp is then held until the current falls naturally. The current limiting feature is active only during the ramp period of the soft start sequence. Closed loop control requires continuous measurement and feed back of the current delivered to the motor terminals by using a CT.
The Dwell period
The dwell period begins when the output voltage reaches maximum and this period is equal to the selected ramp time, approximately equal to 10 seconds.
The dwell period maintains a constant voltage at maximum to allow the time for the motor and its driven load to settle to a steady state after acceleration is complete and before the Soft starter automatically enters the energy optimizing mode.
The optimizing stage
The energy optimizing stage is the normal operating condition of the Soft starter when the motor is up to rated speed and driving the load at whatever torque output is demanded. The energy optimizing stage is continuous after the dwell period until a stop command is given.
During the ramp period the system computes a reference value of the power factor. For energy optimizing this value is continuously compared with the running power factor. From the comparator output the system continuously computes, adjusts and updates the firing points of the thryistors so that the total energy delivered to motor corresponds to the load torque demand without wasting energy in overfluxing the motor. The power factor at the supply terminals is in this way maintained at the highest possible value for every condition of the load demand.
Management of the power factor in no way detracts from the capability of the motor to respond to the load demand .The motor performance is unaffected. This feature of the Soft starter is a purely electric function which has the effect of ensuring that at all times the motor delivers the torque demanded, but is allowed to draw only the precise amount of magnetizing current required to support the torque output.
Without this feature, the motor would draw a maximum magnetizing current regardless of the load.
The effect of the energy optimizing function is a cumulative economy in energy consumption.
The Soft-Stop function
This is a unique feature of the Soft starter. Its effect is to prevent an undesirably sudden deceleration of the load. It is useful in various mechanical handling and conveyor systems and in many hydraulic pumping operations where a sudden removal of the drive input can induce undesirable effects, such as the fluid hammer in the pipelines.
The soft stop ramp operates to reduce the motor terminal voltage down to 40% of maximum, at which time, the thyristors are disabled. The motor and load will coast to standstill.
Post a Comment:
You may also like: